Fatigue analysis is the process of determining the structural integrity of a material or component under repeated loads or cycles over a period of time. The goal of fatigue analysis is to predict when a material or component will fail due to fatigue, so that appropriate measures can be taken to prevent or mitigate the failure. This can include design changes, material selection, and maintenance schedules. Fatigue analysis can be done using a variety of methods, including experimental testing and numerical simulation.
Fatigue analysis is an important aspect of the design and maintenance of structures and components that are subjected to repeated loads or cycles over time. These can include everything from bridges and buildings to aircraft, automobiles, and mechanical systems. Fatigue failure occurs when a material or component experiences repeated loading and unloading, causing small cracks to form and eventually grow until the material or component fails.

Fatigue Analysis Method
There are several methods used to perform fatigue analysis, including:
- S-N (Stress-Life) Method: This method of fatigue analysis plots the stress amplitude (S) against the number of cycles to failure (N). It is the most commonly used method in fatigue analysis. It is based on the assumption that the material is linear-elastic and isotropic.
- Rain flow counting method: This method is used to determine the number of cycles of a given stress range in a non-periodic signal. It is used to convert the stress history into a set of alternating stress cycles.
- Miner’s rule: This method is used to determine the fatigue damage caused by a stress cycle with varying amplitudes. It is used to predict the fatigue life of a material or component based on its microstructure, composition, and loading conditions.
- Linear damage rule (LD) method: This method of fatigue analysis is used to determine the fatigue damage caused by a stress cycle with varying amplitudes. It is based on the cumulative damage caused by the cycles and the material’s fatigue limit.
- Strain-Life Method: This method plots the strain amplitude (ε) against the number of cycles to failure (N). It is used for materials that exhibit plastic deformation or for components with complex geometries.
- FEM (Finite Element Method) based analysis: This method of fatigue analysis uses numerical simulation to predict the behavior of a material or component under repeated loads. It is widely used in fatigue analysis due to its ability to model complex geometries and loading conditions.
- Fatigue crack growth analysis: this method is used to predict the crack growth rate of a material or component under cyclic loading. This can be done by using different models such as Paris law, Walker model, etc.
Types of Fatigue
There are several types of fatigue, including:
- High cycle fatigue (HCF)
- Low cycle fatigue (LCF)
- Fatigue crack initiation
- Fatigue crack propagation
- Thermal fatigue
- Corrosion fatigue
- Fatigue under complex loading
- Fatigue under multiaxial loading

High Cycle Fatigue (HCF):
This type of fatigue occurs when a material or component experiences a large number of cycles, typically more than one million cycles, at a relatively low stress amplitude. In HCF, failure is caused by the initiation and growth of small cracks in the material or component. These small cracks can eventually grow and lead to failure. HCF is typically associated with components that experience a large number of cycles at relatively low stress levels, such as aircraft turbine blades, gears, and ball bearings.
Low Cycle Fatigue (LCF):
This type of fatigue occurs when a material or component experiences a small number of cycles, typically less than one million cycles, at a relatively high stress amplitude. In LCF, failure is typically caused by plastic deformation or ductile fracture, rather than by crack initiation and growth. LCF is typically associated with components that experience a small number of cycles at relatively high stress levels, such as landing gear, crane booms, and heavy machinery components.
Fatigue Crack Initiation:
This type of fatigue occurs when small cracks form in a material or component due to repeated loading. These cracks can eventually grow and lead to failure. Fatigue crack initiation is typically associated with HCF, but can also occur in LCF if the stress amplitude is high enough.
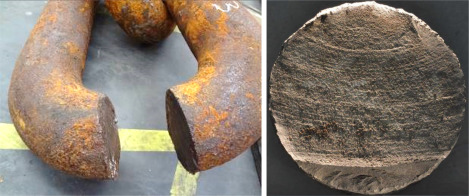
Fatigue Crack Propagation:
This type of fatigue occurs when existing cracks in a material or component grow due to repeated loading. This type of fatigue is typically associated with HCF, but can also occur in LCF if the stress amplitude is high enough. Fatigue crack propagation can be modelled using various techniques such as Paris law, Walker’s model and etc.
Thermal Fatigue:
This type of fatigue occurs when a material or component is subjected to alternating high and low temperatures. It can be caused by temperature cycles, thermal gradients, and other heat-related factors. Thermal fatigue can lead to the formation of small cracks in the material or component, which can eventually grow and lead to failure.
Corrosion Fatigue:
This type of fatigue occurs when a material or component is exposed to both cyclic loading and a corrosive environment. The corrosion can weaken the material, making it more susceptible to fatigue failure. Corrosion fatigue can occur in both HCF and LCF, and can lead to a reduction in the fatigue life of the material or component.
Fatigue Under Complex Loading:
This type of fatigue occurs when a material or component is subjected to a combination of different types of loading, such as cyclic loading, thermal loading, and mechanical loading. The interaction between these different types of loading can lead to more complex failure mechanisms and different fatigue behavior.
Fatigue Under Multiaxial Loading:
This type of fatigue occurs when a material or component is subjected to different types of loading in multiple directions. This can lead to more complex failure mechanisms and different fatigue behavior. Multiaxial loading can also lead to more severe stress concentrations, which can accelerate fatigue crack initiation and propagation.
Reason of Fatigue Analysis
There are several reasons why fatigue analysis can occur in materials and components, including:
- Repeated loading: Fatigue analysis occurs when a material or component is subjected to repeated loading, causing small cracks to form and eventually grow until the material or component fails.
- High stress levels: High stress levels can lead to the formation of small cracks in a material or component, which can eventually grow and lead to failure.
- Material properties: The properties of a material, such as its microstructure, composition, and hardness, can affect its susceptibility to fatigue.
- Environmental factors: Exposure to certain environmental factors, such as temperature changes, humidity, and corrosive environments, can affect the fatigue life of a material or component.
- Surface finish: Surface finish can also play a role in fatigue. Surface imperfections can act as stress concentrators and accelerate fatigue crack initiation.
- Design : poor design can lead to high stress concentration points and this can increase the susceptibility of the component to fatigue.
- Manufacturing defects: Manufacturing defects, such as inclusions, porosity, and surface defects, can affect the fatigue life of a material or component.
- Load history : The load history of a component can also affect its fatigue life. For example, a component that has been loaded to its maximum capacity may have a shorter fatigue life than one that has never been loaded to capacity.
- Multiaxial loading: A material or component that is subjected to different types of loading in multiple directions may experience more complex failure mechanisms and different fatigue behavior.
- Complex loading: A material or component that is subjected to a combination of different types of loading, such as cyclic loading, thermal loading, and mechanical loading, may experience more complex failure mechanisms and different fatigue behavior.

Factors Effecting Fatigue Behavior
There are several factors that can affect the fatigue behavior of a material or component, including:
- The amplitude of the stress that a material or component is subjected to can affect its fatigue behavior
- Stress concentrations can occur at certain points on a material or component, such as corners and edges
- Mean stress can affect the fatigue behaviour of a material or component, particularly if the mean stress is close to the material’s yield strength.
- Temperature changes can affect the fatigue behavior of a material or component.
- The frequency of loading can affect the fatigue behavior of a material or component. Higher frequency loading can lead to higher stress amplitudes and more cycles, which can accelerate fatigue crack initiation and propagation.
- Surface finish can also play a role in fatigue. Surface imperfections can act as stress concentrators and accelerate fatigue crack initiation.
- Corrosion can affect the fatigue behavior of a material or component by weakening the material and making it more susceptible to fatigue failure.
Failure Criteria of Fatigue Analysis
There are several failure criteria that are used in fatigue analysis to predict when a material or component will fail due to fatigue, including:
- Maximum stress criterion: This criterion states that a material or component will fail when the maximum stress reaches a certain value.
- Minimum stress criterion: This criterion states that a material or component will fail when the minimum stress reaches a certain value.
- Mean stress criterion: This criterion states that a material or component will fail when the mean stress reaches a certain value.
- Endurance limit criterion: This criterion states that a material or component will not fail if the stress amplitude is below a certain value, called the endurance limit.
- Fracture mechanics criterion: This criterion states that a material or component will fail when a crack reaches a certain size and the stress intensity factor exceeds the material’s fracture toughness.
- Fatigue damage criterion: This criterion states that a material or component will fail when the accumulated damage from cyclic loading reaches a certain value.
Factors that can affect the fatigue analysis behavior of a material or component include stress amplitude, stress concentration, mean stress, temperature, frequency of loading, surface finish, load history, corrosion and microstructure. To predict when a material or component will fail due to fatigue, several failure criteria are used, including maximum stress criterion, minimum stress criterion, mean stress criterion, stress-life criterion, strain-life criterion, endurance limit criterion, fracture mechanics criterion and fatigue damage criterion.