Piping systems are the backbone of industrial facilities, from petrochemical plants to power stations. These systems must withstand various stresses and environmental conditions to operate safely and efficiently. Two critical theories dominate the analysis of material failure in piping systems: the Tresca Yield Criterion and the Von Mises Yield Criterion. While these theories have been extensively discussed in the context of material science and mechanical engineering, their specific applications in piping engineering provide an interesting perspective.
This blog dives deep into the nuances of Tresca and Von Mises, discussing their applications, benefits, and limitations in the world of piping engineering.
Understanding the Basics
Piping systems are subject to a combination of stresses, including axial, circumferential (hoop), and radial stresses, arising from internal pressure, temperature changes, and external forces. To ensure the structural integrity of the pipes, engineers rely on yield criteria to predict when a material will fail under these complex stress states.
Tresca Yield Criterion: The Conservative Approach
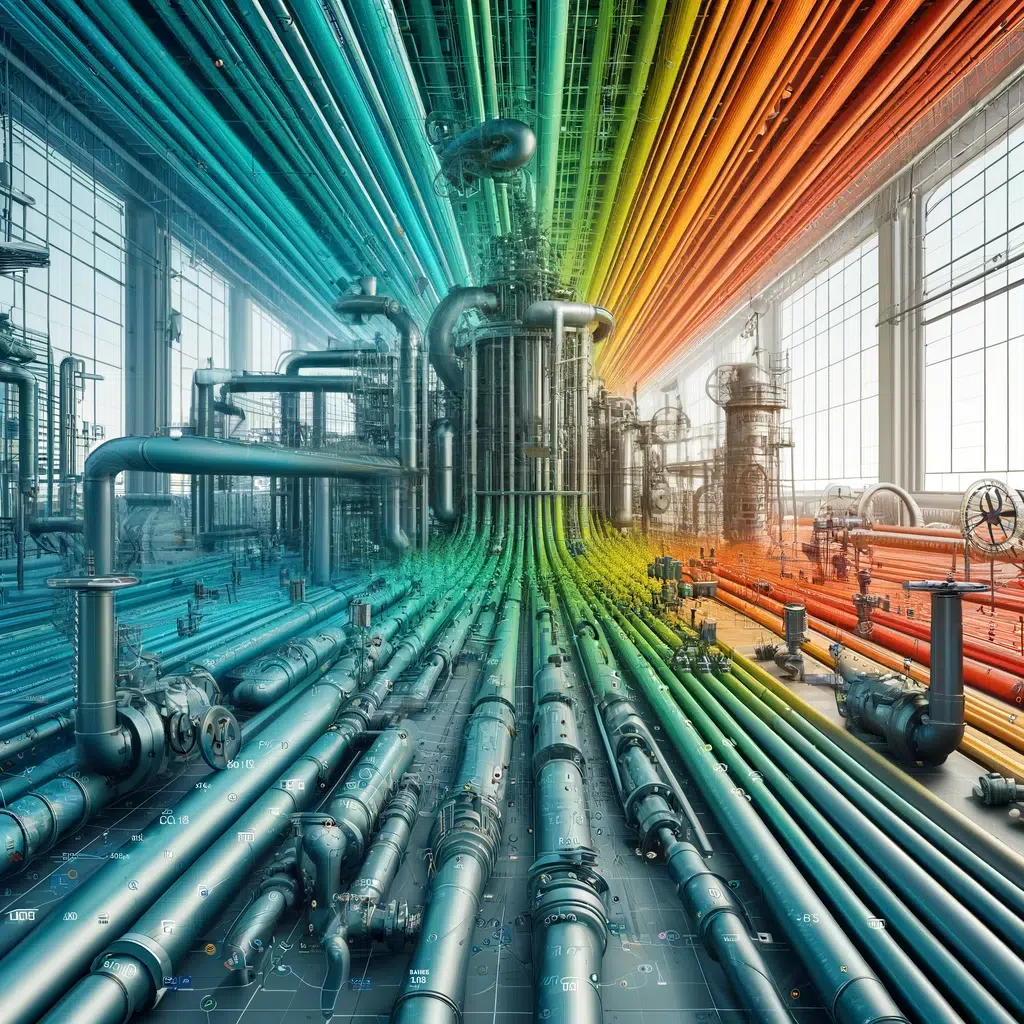
The Tresca Yield Criterion, also known as the Maximum Shear Stress Theory, is a straightforward method to predict material failure. It assumes that a material will yield when the maximum shear stress in the system exceeds a critical value determined from the material’s yield strength.
In piping engineering, Tresca is particularly effective in scenarios where the shear stress is dominant, such as:
- High-pressure systems.
- Components with abrupt geometric changes, like tees, elbows, or welded joints.
- Thin-walled pipes under internal pressure.
The Tresca approach is favored in many cases because of its simplicity. By focusing on the maximum shear stress, it provides a conservative estimate of the material’s ability to withstand loads. This conservative nature makes Tresca a reliable tool in safety-critical applications where over-design is preferable to underestimating potential failure.
Von Mises Yield Criterion: The Accurate Predictor
The Von Mises Yield Criterion, also known as the Distortion Energy Theory, provides a more nuanced view of material failure. It considers the total distortion energy in a material, making it more suitable for complex, multi-axial stress states.
In the context of piping systems, Von Mises is often used for:
- Thick-walled pipes where the stress distribution is more intricate.
- Components subjected to combined loading conditions, such as axial tension and internal pressure.
- Finite Element Analysis (FEA) of piping systems, where accuracy is crucial.
Von Mises is less conservative than Tresca, allowing for more efficient use of materials. This makes it a preferred choice for detailed engineering analyses, particularly in cost-sensitive projects where reducing material thickness without compromising safety is a priority.
Applications in Piping Engineering
The choice between Tresca and Von Mises often depends on the specific requirements of the piping system, the criticality of the application, and the complexity of the stress states involved.
When to Use Tresca?
Tresca’s simplicity and conservatism make it a go-to option for:
- Preliminary Design: Early-stage calculations often involve simplified assumptions to quickly determine the feasibility of a design. Tresca’s ease of use makes it ideal for these scenarios.
- Safety-Critical Systems: In industries like nuclear power or petrochemicals, safety margins are paramount. Tresca’s conservative nature ensures that potential failures are addressed well before they occur.
- Localized Stress Analysis: Components like nozzles, gaskets, and flanges often experience localized stress concentrations. Tresca’s focus on maximum shear stress makes it particularly effective in identifying these potential weak points.
When to Use Von Mises?
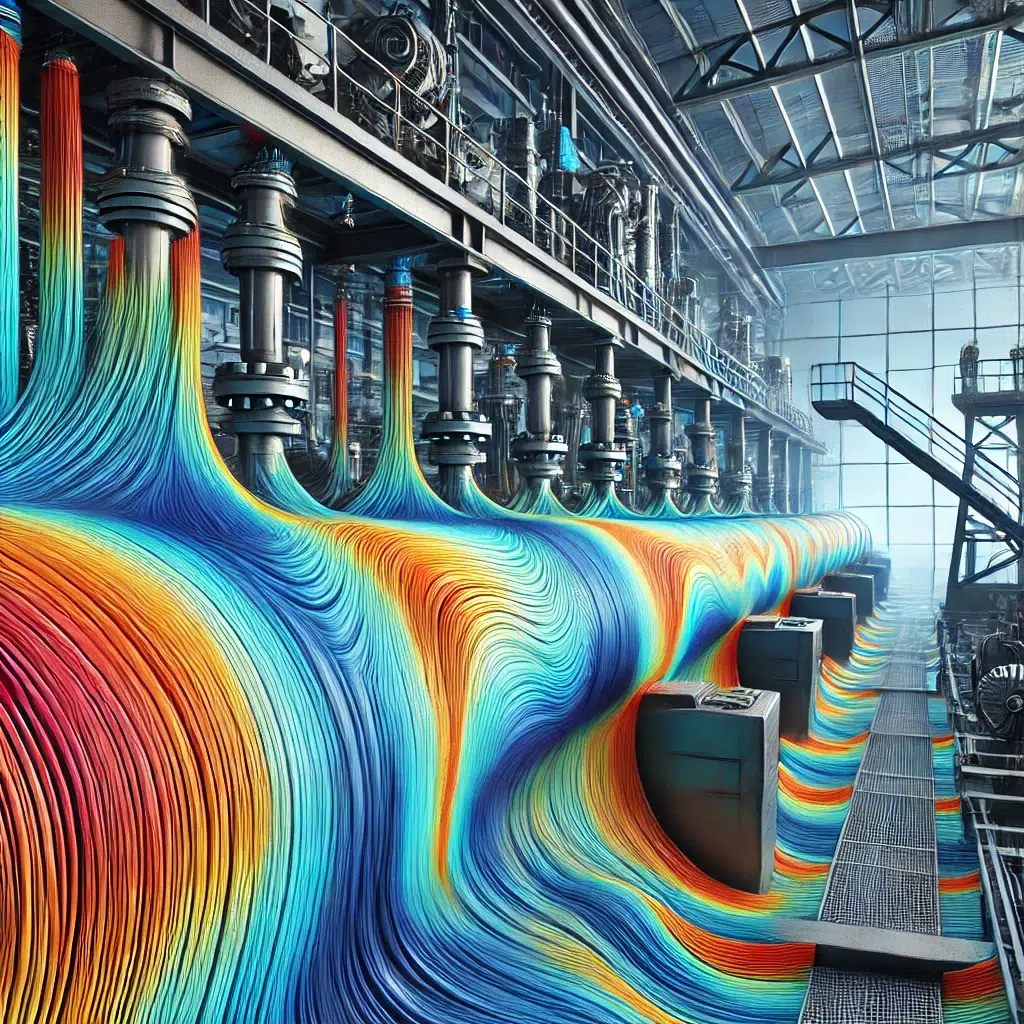
Von Mises is the preferred choice in scenarios requiring detailed analysis and material optimization:
- Thick-Walled Pipes: Unlike thin-walled pipes, thick-walled systems experience non-uniform stress distributions. Von Mises provides a more accurate prediction of yielding in such cases.
- High-Temperature Applications: Systems operating under extreme temperatures often experience complex stress states due to thermal expansion. Von Mises is better equipped to handle these scenarios.
- Finite Element Analysis: Modern engineering relies heavily on computational tools like FEA to analyze stresses in piping systems. Von Mises integrates seamlessly into these tools, offering precise results under multi-axial stress conditions.
Comparative Insights
While both Tresca and Von Mises are widely used, their differences significantly influence their applicability in piping engineering. Understanding these differences is essential for selecting the appropriate criterion.
- Conservatism:
- Tresca provides a more conservative estimate of failure. This is advantageous in safety-critical systems where over-design is acceptable.
- Von Mises, being less conservative, is better suited for optimizing material usage in cost-sensitive projects.
- Complexity:
- Tresca is straightforward, requiring fewer computational resources. It is ideal for quick checks or manual calculations.
- Von Mises is more complex but offers higher accuracy, especially for systems under combined loads.
- Applications:
- Tresca is favored for localized stress analysis and preliminary design phases.
- Von Mises is preferred for detailed engineering analyses and high-precision FEA models.
Practical Example: Piping Under Internal Pressure
To understand the practical application of Tresca and Von Mises yield criteria, let us consider a pipeline designed to transport high-pressure gas. This pipeline, typically made of steel or similar ductile materials, is subjected to various stresses caused by the internal pressure of the gas, external loads, and environmental factors. These stresses include axial stress (along the length of the pipe), circumferential or hoop stress (around the pipe’s diameter), and radial stress (perpendicular to the surface of the pipe wall). The combination of these stresses determines the overall loading condition.
Engineers must ensure that the pipeline material can withstand these stresses without yielding. Yielding would compromise the integrity of the pipeline, leading to deformation, leaks, or catastrophic failure. This is where the Tresca and Von Mises yield criteria come into play to assess whether the pipeline design is safe and optimized.
Tresca Criterion in Practice
The Tresca criterion, also called the Maximum Shear Stress Theory, is a relatively simple and conservative approach to predicting material failure. In this example, the engineer focuses on the maximum shear stress within the pipeline wall. Shear stress arises when different layers within the material slide relative to one another, and it is critical in preventing material deformation.
Application:
- Shear Stress Calculation: The engineer calculates the maximum and minimum principal stresses (σ1 and σ3) within the pipeline material. The Tresca criterion identifies yielding when the difference between these principal stresses exceeds the material’s shear yield strength.
- Design Implications: If the calculated maximum shear stress exceeds the critical value, the material is deemed to have yielded. In response, the engineer may increase the pipe’s wall thickness, select a stronger material, or reduce the operating pressure to ensure safety.
Advantages in This Scenario:
- Simplicity: Tresca’s focus on maximum shear stress allows engineers to quickly evaluate whether the pipeline design is safe, especially during the preliminary design phase.
- Conservatism: By predicting failure earlier, Tresca ensures a higher safety margin, which is crucial in high-pressure systems where any failure could have catastrophic consequences.
Example Outcome:
Let’s assume the pipeline is designed to transport gas at 150 bar pressure. Using Tresca, the engineer determines that the maximum shear stress in the pipe wall is close to the critical value. To stay on the safe side, the engineer increases the wall thickness by 10%. While this may increase material and manufacturing costs, it ensures the pipeline operates well within safe limits, preventing potential disasters.
Von Mises Criterion in Practice
The Von Mises criterion, or the Distortion Energy Theory, takes a more detailed approach by evaluating the total energy required to distort the material. This method considers all three principal stresses (σ1, σ2, and σ3) and calculates an equivalent stress, often referred to as Von Mises stress. If this equivalent stress exceeds the material’s yield strength, the material is considered to have yielded.
Application:
- Stress Analysis: Using advanced computational tools like Finite Element Analysis (FEA), the engineer evaluates the stress distribution across the pipe wall. Von Mises stress is calculated by combining the effects of axial, circumferential, and radial stresses.
- Material Optimization: Unlike Tresca, which may lead to over-design, Von Mises allows for a more accurate assessment. If the Von Mises stress is below the yield strength, the engineer can safely reduce the pipe’s wall thickness, potentially lowering material and manufacturing costs without compromising safety.
Advantages in This Scenario:
- Accuracy: Von Mises provides a realistic picture of how the material behaves under multi-axial stress states, leading to optimized designs.
- Material Savings: By avoiding the conservative assumptions of Tresca, Von Mises enables engineers to minimize material usage while ensuring safety.
Example Outcome:
For the same pipeline transporting gas at 150 bar, the Von Mises analysis reveals that the equivalent stress is well below the material’s yield strength. This allows the engineer to reduce the wall thickness by 5% compared to the Tresca-based design. The thinner pipe meets safety standards, reduces costs, and lowers the overall weight of the pipeline, which is advantageous for transportation and installation.
Real-World Implications: Choosing Between Tresca and Von Mises

In real-world scenarios, the decision to use Tresca or Von Mises depends on several factors, including the criticality of the application, cost considerations, and the complexity of the loading conditions.
- High-Pressure Gas Transmission Lines:
- For pipelines transporting hazardous or flammable gases, Tresca is often used during the initial design phase to ensure an ample safety margin. The additional material thickness provided by Tresca’s conservative nature is acceptable in exchange for increased safety.
- Once the design is finalized, Von Mises may be applied for a detailed analysis. This step helps identify areas where the material can be optimized, ensuring cost-efficiency without compromising safety.
- High-Temperature Applications:
- Pipelines operating under extreme temperatures are more prone to thermal expansion and complex stress states. Von Mises is better suited for these applications due to its ability to account for distortion energy.
- Localized Stress Concentrations:
- In areas of the pipeline where stress concentrations are significant, such as welded joints or bends, Tresca’s focus on shear stress makes it a reliable choice. However, combining Tresca with Von Mises in such cases can provide a comprehensive understanding of potential failure points.
Modern Approaches: Balancing Tresca and Von Mises in Piping Engineering
Modern engineering practices often require a balance between safety, cost-efficiency, and the ability to adapt to complex stress scenarios. By leveraging both Tresca and Von Mises yield criteria strategically, piping engineers can ensure robust designs without excessive material usage. This dual approach reflects the evolution of piping engineering, where initial safety considerations and advanced computational techniques work hand-in-hand.
Using Tresca as a Conservative Baseline
In the initial stages of designing a piping system, Tresca is often the preferred method. Its simplicity and conservatism allow engineers to quickly establish a safety baseline without delving into complex calculations. This stage focuses on ensuring the pipeline will perform under worst-case scenarios.
Key Advantages of Using Tresca Initially:
- Quick Estimation:
- Tresca provides a straightforward approach to assessing the pipe’s capacity to withstand stresses, making it ideal for preliminary designs.
- By focusing on maximum shear stress, it highlights areas that could potentially fail, ensuring that critical components like elbows, tees, or welded joints are adequately reinforced.
- High Safety Margins:
- Tresca’s conservative nature errs on the side of caution, making it particularly suitable for safety-critical systems, such as pipelines carrying high-pressure steam, hazardous chemicals, or flammable gases.
- Baseline for Cost Comparisons:
- Using Tresca allows engineers to define an initial design that guarantees safety. This serves as a reference point for further refinement using more advanced methods like Von Mises.
Example in High-Pressure Steam Systems:
In a high-pressure steam pipeline, Tresca is used to calculate the required wall thickness to handle internal pressure safely. The design may call for a pipe with an initial thickness of, say, 20 mm, based on Tresca’s conservative estimates. This thickness ensures the pipeline can withstand extreme operational conditions, including pressure surges or thermal stresses.
Employing Von Mises for Refinement and Optimization
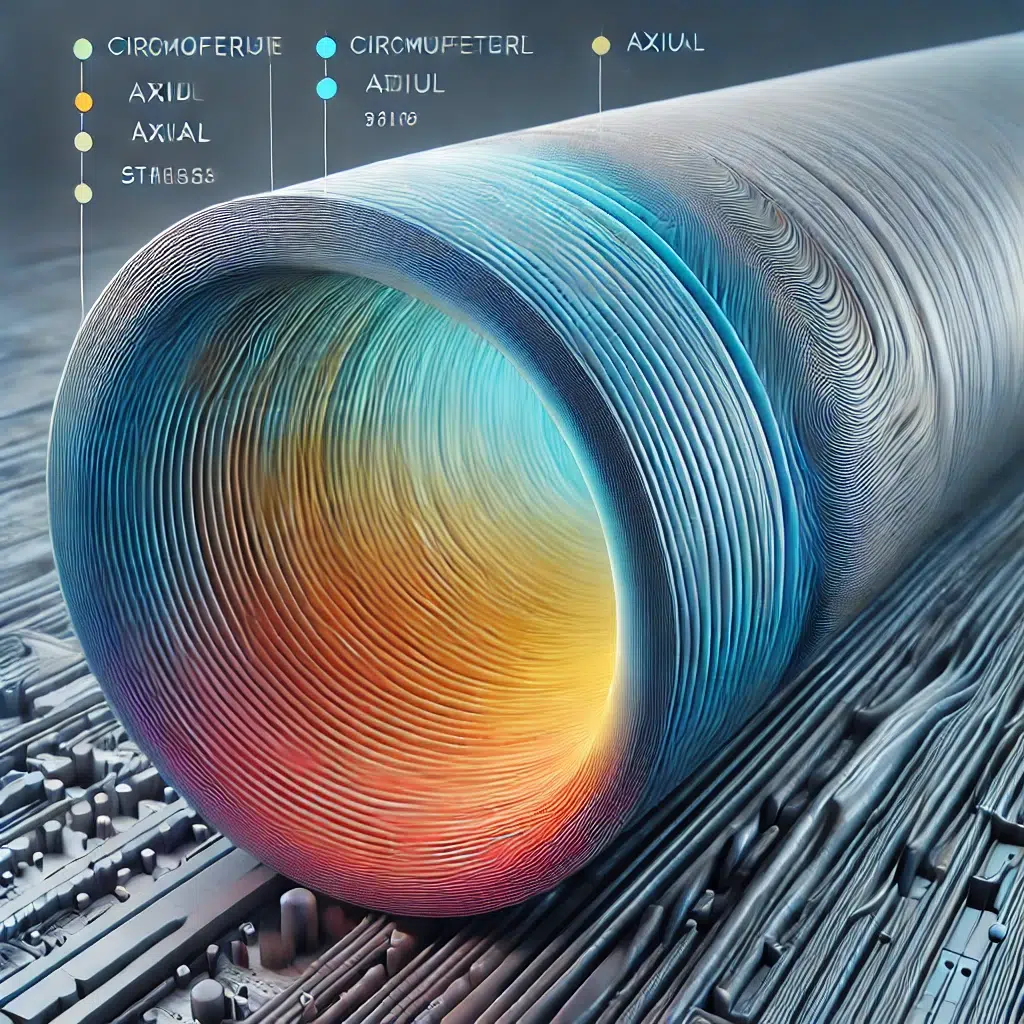
Once the initial design is validated for safety using Tresca, engineers can refine the design with Von Mises. The Distortion Energy Theory offers a more accurate assessment of material behavior under complex, multi-axial stress states. This step allows for significant optimization in terms of material usage and overall cost.
Advantages of Refining with Von Mises:
- Accurate Stress Analysis:
- Von Mises evaluates the combined effect of axial, circumferential, and radial stresses, providing a realistic picture of how the material will behave under actual operating conditions.
- It is particularly effective in identifying areas where the pipe experiences lower-than-expected stresses, which can then be optimized.
- Material Optimization:
- By avoiding the conservative assumptions of Tresca, Von Mises enables engineers to reduce wall thickness, lower material costs, and minimize weight, which is critical for transportation and installation.
- Integration with Advanced Tools:
- Modern Finite Element Analysis (FEA) tools are designed to work seamlessly with Von Mises. These tools allow engineers to simulate real-world loading scenarios, including temperature gradients, external forces, and internal pressure variations.
Example of Refinement:
Returning to the high-pressure steam pipeline example, detailed analysis using Von Mises may reveal that the 20 mm wall thickness calculated by Tresca is over-designed. The equivalent stress calculated by Von Mises might allow for a reduction to 17 mm, while still maintaining safety. This 15% reduction in material thickness translates to significant cost savings, especially in large-scale pipeline projects.
The Combined Approach in Modern Piping Design
The dual use of Tresca and Von Mises reflects a structured and efficient workflow in piping engineering:
- Preliminary Design with Tresca:
- Tresca is used as a “first-pass” analysis tool to identify high-stress areas and establish a safety margin.
- This ensures that the system meets regulatory requirements and accounts for uncertainties in operating conditions.
- Detailed Optimization with Von Mises:
- Von Mises is applied in the later stages to refine the design, focusing on efficiency and cost-effectiveness without compromising safety.
- Advanced simulations may include scenarios like pressure pulsations, thermal expansion, and external mechanical loads.
Real-World Applications of the Combined Approach
1. Oil and Gas Pipelines:
- Tresca is used initially to design pipelines that can handle high-pressure oil or gas transport over long distances.
- Von Mises is employed later to optimize the material, ensuring the pipeline remains cost-effective without compromising on reliability.
2. Chemical Processing Plants:
- In chemical processing, pipelines often transport corrosive or volatile fluids. Tresca helps ensure a robust design to account for internal pressure and potential surges.
- Von Mises helps refine the design, reducing material usage while maintaining resistance to failure under combined stresses.
3. Power Plants:
- High-pressure steam pipelines in power plants undergo both thermal and mechanical stresses. Tresca provides a conservative baseline to ensure safety in extreme conditions.
- Detailed FEA using Von Mises allows engineers to optimize the design, balancing safety and efficiency.
The example of a high-pressure gas pipeline illustrates the importance of Tresca and Von Mises criteria in piping engineering. While Tresca ensures safety with its conservative approach, Von Mises allows engineers to push the boundaries of material efficiency. In practice, combining these criteria provides the best of both worlds—robust designs that are both safe and cost-effective. Whether you’re designing pipelines for hazardous chemicals, steam transport, or natural gas, understanding the strengths and applications of Tresca and Von Mises can make all the difference in achieving engineering excellence.